Revolutionizing Design – The Impact of 3D Prototyping on Modern Manufacturing
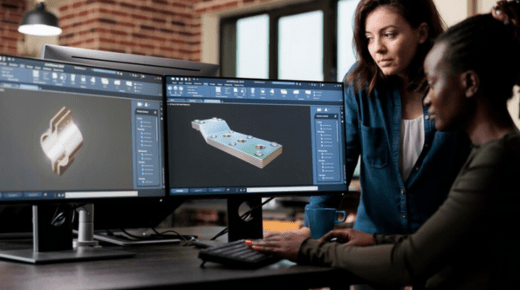
In the realm of modern manufacturing, 3D prototyping stands out as a game-changing technology that is reshaping the way products are designed and developed. This innovative process, which involves creating three-dimensional models from digital designs, has introduced unprecedented efficiencies and possibilities to industries across the board. The transformative effects of 3D prototyping on manufacturing are profound, affecting everything from product development cycles to cost management and design precision.
The Evolution of Prototyping
Traditionally, prototyping was a time-consuming and costly phase in the product development process. Engineers and designers had to rely on manual methods or complex machinery to create physical prototypes, which often involved multiple iterations and significant material waste. With the advent of 3d prototyping, these challenges have been mitigated through the use of advanced digital technologies.
3D prototyping leverages computer-aided design (CAD) software to generate detailed three-dimensional models. These models are then used to create physical prototypes through additive manufacturing techniques, such as 3D printing. This approach allows for rapid iteration and refinement, significantly speeding up the development process.
Accelerating Product Development
One of the most notable impacts of 3D prototyping on modern manufacturing is the acceleration of product development cycles. By enabling designers to quickly produce and test prototypes, 3D prototyping reduces the time required to move from concept to market-ready product. This accelerated pace allows companies to respond more swiftly to market demands and stay ahead of the competition.
For example, in the automotive industry, manufacturers can use 3D prototyping to rapidly test and refine new vehicle designs. Instead of waiting weeks or months for traditional prototypes, engineers can produce functional models in a matter of days. This agility not only speeds up the development process but also enhances the ability to innovate and adapt to changing consumer preferences.
Enhancing Design Precision
Another significant advantage of 3D prototyping is its ability to enhance design precision. Traditional prototyping methods often involve manual adjustments and refinements, which can introduce errors and inconsistencies. In contrast, 3D prototyping allows for highly accurate and detailed representations of designs.
With 3D prototyping, designers can visualize and test their concepts in a realistic and interactive manner. The ability to examine prototypes from multiple angles and perspectives ensures that design flaws are identified and addressed early in the development process. This level of precision not only improves the overall quality of the final product but also reduces the risk of costly design errors.
Reducing Costs and Waste
Cost management is a critical consideration in manufacturing, and 3D prototyping offers significant benefits in this regard. Traditional prototyping methods often involve substantial material and labor costs, especially when multiple iterations are required. 3D prototyping, on the other hand, minimizes material waste by using only the necessary amount of material for each prototype.
Additive manufacturing techniques used in 3D prototyping build objects layer by layer, resulting in minimal material waste compared to subtractive methods. This reduction in waste not only lowers production costs but also contributes to more sustainable manufacturing practices.
Fostering Innovation
The impact of 3D prototyping extends beyond efficiency and cost savings. By providing designers with the tools to experiment and explore new ideas, 3D prototyping fosters a culture of innovation. Designers can easily test unconventional concepts and push the boundaries of traditional design, leading to the development of novel products and solutions.
In industries such as aerospace and healthcare, where complex and highly specialized components are required, 3D prototyping enables the creation of intricate designs that were previously impractical or impossible. This newfound flexibility in design opens up new possibilities for innovation and problem-solving.
The Future of 3D Prototyping
As technology continues to advance, the future of 3D prototyping promises even greater enhancements to the manufacturing process. Emerging technologies such as advanced materials and multi-material 3D printing are expected to further expand the capabilities of 3D prototyping. Additionally, the integration of artificial intelligence and machine learning could streamline design processes and improve prototype accuracy.
The widespread adoption of 3D prototyping is likely to continue transforming the manufacturing landscape. As more industries recognize the benefits of this technology, its applications will become increasingly diverse, leading to even greater innovations and efficiencies.
Conclusion
3D prototyping has revolutionized modern manufacturing by accelerating product development, enhancing design precision, reducing costs and waste, and fostering innovation. Its impact on the industry is profound, offering new opportunities for designers and manufacturers to create high-quality products more efficiently and sustainably. As technology continues to evolve, the potential for 3D prototyping to drive further advancements in manufacturing is boundless, marking an exciting era of transformation and progress.